Policy and Strategy
Basic Views
Our Corporate Philosophy states that safety will always come first, while the IINO Group Sustainability Policy states that "The IINO Group places our highest management priority on ensuring safety." We aim to ensure the safety of its employees and business partners, including subcontractors. Because we are acutely aware of the harm that could be caused to life, customer resources, and the environment by any negligence in our shipping or real estate operations, we will constantly strive to eliminate accidents of all kinds. It is based on these principles that we strive to ensure the safety of our employees as well as business partners, including contractors. We investigate the cause of accidents or disasters that imperil people's lives or the safety of ships and buildings in connection with our business activities, discuss measures to prevent repeat occurrences, and strive to thoroughly strengthen safety measures, including preventative action. Our main targets for FY2024 have been set as zero accidents per ship in the Shipping Business and an occupational accident frequency rate of 0.4 or less among crew members. In the Real Estate Business, we have set targets of zero employees certified as having suffered occupational accidents at IINO Building Technology Co., Ltd. (IBT) and the reduction of other accidents and mishaps (accidents due to human factors: 0 or less, accidents due to equipment or facilities: 0 or less). Additionally, in the Group's mid-term management plan, we have declared the non-financial numerical target of zero serious accidents (achieving a result of 0 accidents in FY2023) and make proactive efforts to ensure safety.
Structure
Supervision of Safety at the Director Level
To deal with accidents and disasters that have occurred within the IINO Group, we have established a Safety and Environment Committee (permanently established in accordance with Safety and Environment Committee Regulations) chaired by the President and Representative Director and comprising Company directors as regular members. The committee investigates the cause of accidents or disasters, discusses measures to prevent repeat occurrences, and strives to thoroughly strengthen safety measures, including preventative action. Particularly in emergency situations such as damage to the environment from oil pollution, major accidents, and other mishaps involving people's lives or property, and major disasters, in accordance with our Risk Management Rules, we set up an Emergency Headquarters led by the President and Representative Director and engage in crisis management.
Risk Assessment of Labor Issues
We monitor working hours and health to ascertain risks related to the occupational safety of employees and take action aimed at improvements after sharing information between labor, management, and the managers of each division.
Initiatives
Dialogue between Labor and Management
The Company respects employees' right to organize and right to collective bargaining as a means of labor-management negotiations. IINO LINES and IINO LINES Labor Union regularly make opportunities to engage in dialogue on the development of the Company and the facilitation of its labor/management relations and business activities. A joint labor-management health and safety committee meeting is held monthly to provide an opportunity for dialogues between representatives from labor and management where they exchange views on a variety of issues such as working hours management and occupational safety and health. Opportunities are also established to exchange views on a wide range of topics as needed, including the secondment and salaries of union members, and wage systems such as allowances. Labor and management work together to improve employees' health and safety while developing a comfortable workplace environment. The union membership ratio of the Company's onshore employees is 100%.
Initiatives to Address Bullying and Harassment
Once a year, corporate lawyers are invited to conduct workshops for the IINO Group officers and employees on the prevention of harassment. The workshops include definitions and descriptions of cases of harassment, prevention measures, information about consultation services when harassment has occurred, and how to prepare yourself to receive consultations about harassment. This is part of efforts to raise awareness about harassment among officers and employees in the workplace.
Additionally, regulations concerning the prevention of sexual harassment and power harassment, reporting system based on Compliance Regulations and a external whistleblower system* has been established such that if officers and employees of the Group (including board members, permanent employees, contract workers, contract employees, temporary employees, seconded employees and part-timers, and retirees), and business partner of the Group discover illegal or unethical actions, or have reason to suspect such actions are taking place, the Company will quickly confirm the facts, and engage in appropriate corrective measures.
* For details, please check the section on Ensuring Thorough Compliance.
Occupational Health and Safety at IINO LINES
IINO LINES provides periodic health checkups twice a year. We also set aside meeting rooms once a month to offer individual consultations with occupational physicians.
Status of Occupational Accidents
In FY2023, no occupational accidents occurred at IINO LINES, IBT, or IINO Marine Service Co., Ltd. (IMS*).
* Excluding IMS crew members
Safety in the Shipping Business
Based on the conviction that safety is the foundation of our business operations, the IINO Group takes various measures to ensure safety in the Shipping Business.
Overview of Major Policies Concerning Safety
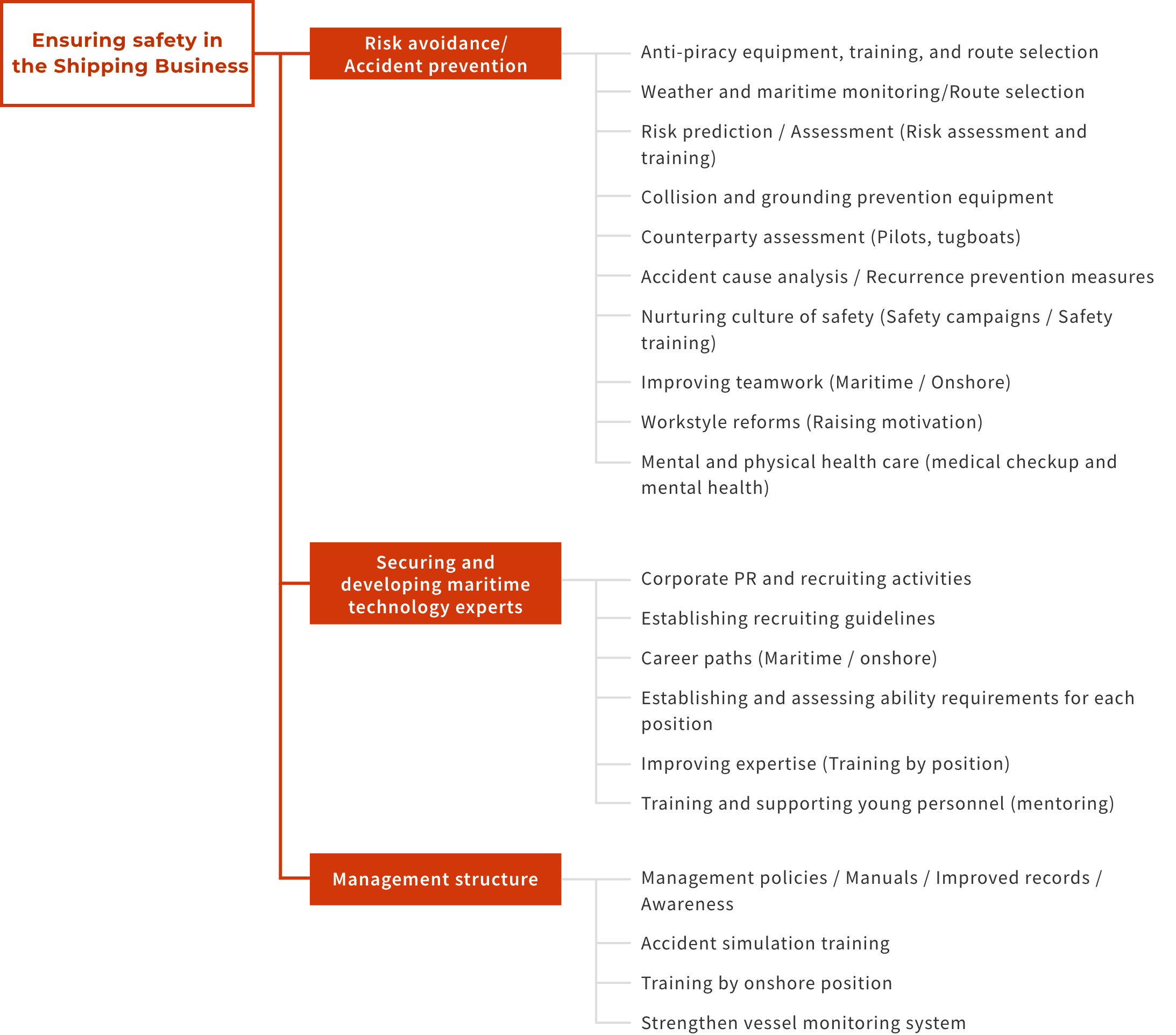
Nurturing Culture of Safety (Safety Campaigns / Safety Training)
We believe that proactive safety activities by officers and employees at sea and on land are essential to ensuring the safe operation of vessels. For this reason as a safety campaign, the President and other members of management make ship visits to strengthen cooperation between maritime and onshore officers and employees through dialogue, improve staff loyalty, and improve safety awareness. These ship visit activities afford a valuable opportunity for management to grasp the challenges and views of the workplace. Note that during the COVID-19 pandemic, instead of conducting ship visits, we distributed safety campaign videos and actively gathered opinions and issues from those in the field through dialogue between the crew and management through online meetings between personnel at sea and on land.
Additionally, three times a year in South Korea and the Philippines, twice a year in Japan, India and Myanmar, we hold safety training for crew members on leave to study safety awareness and safe conduct for further developing a "safety culture".
In recent years, we have focused on: (1) proactive suggestions from subordinates (SPEAK UP), (2) supervisors having an open-minded attitude to listening to the views of subordinates (LISTEN UP), (3) mental health, and (4) development and support for young personnel (mentoring).
Conditions required for the safe operation of ships
- At sea
- Placement of required equipment
- Presence of effective manuals
- Assignment of trained crew
- Management of the physical and mental health of crew
- On land
- Establishment of appropriate support systems
- Appropriate revision of manuals, and
- Smooth communication systems between crew and both internal and external related parties
Conditions required for achievement
- Compliance with manuals
- Appropriate operation and support for ships
- Maintaining soundness of equipment through maintenance at the appropriate time
- Safety awareness to ensure communications are made at an early stage
Training for Non-Japanese Crew
IMS strives to maintain vessels consigned by their owners. IMS also arranges the manning of the vessels as required to ready them for operations and carries out crew training. For our non-Japanese crew, the majority of our entire crew, we offer the crew training programs supported by our exclusive companies, IMS KOREA CO., LTD in South Korea and IMS PHILIPPINES MARITIME CORP. in the Philippines. Instructors dispatched by IMS offer short-term training on safety management systems and Kiken Yochi Training (KYT) on a yearly basis to enhance skills for hazard prediction. We also make effective use of online training as needed. IMS continues to implement initiatives utilizing online technologies and other systems to make its organizations resilient to the occurrence of error, including the offering of training programs on human error countermeasures and communication enhancement, and seminars on mental health and mentoring.
Improving Expertise
Maritime technology experts, who play a key role in providing high quality services and securing safety, are required to advance their technological skills and appropriately respond to diversity to secure safety in the four areas of human life, environment, cargo, and vessels.
With the intent of steadily and efficiently developing maritime technology experts, the IINO Group defines abilities and training items that are required of each maritime position and onshore position and implements these as necessary. Through technological training, certification courses, ability improvement training, and internal lectures provided by equipment manufacturers, maritime technology experts are able to acquire knowledge and skills for responding to the demands of changing times and the advancement of technology, as we aim to provide additional safety in our shipping operations.
Meanwhile, it is difficult to secure safety through improving the knowledge and expertise of individual maritime technology experts alone, and onboard the ship, it becomes important to secure safety through the total strength of the team.
As one measure to increase total strength, Bridge Resources Management training* and Engine-room Resource Management training* sessions are held periodically, ultimately leading to safe operations.
* The idea that all available resources (people, things, and information) on the bridge and in the engine room should be managed effectively to achieve safe and efficient ship operation.
Accident simulation training
The IINO Group implements various measures to realize safe shipping operations. However, in the unfortunate event of an accident, it is of the utmost importance to minimize the impact of the accident on human life, the environment, and customers through appropriate first-response measures.
To enable quick first response in the event of an emmergency in the Oceangoing Shipping business, the IINO Group conducts tabletop drills 4 times a year, simulating specific accidents under various circumstances. Members of the emergency response headquarters at the Head Office conduct training in conformity with the Maritime Accident First Response Manual, and the Company ensures that ships and the emergency response headquarters function effectively at the time of an accident. Additionally, after the tabletop drills, a postmortem session is held, which seeks to enable continuous improvement. Additionally, in anticipation of incidents where members of the emergency response headquarters are unable to physically gather, we have partially revised the manual and have begun to set up an emergency response headquarters that makes maximum use of digital tools according to the level of marine accident, as well as to conduct online coordination training for each department. In addition, a press conference drill is conducted on a regular basis with third-party consultants on the assumption that a maritime accident occurred.
Strengthen Vessel Monitoring System
While enhancing anti-piracy equipment on vessels and selecting appropriate routes in cooperation with meteorological information agencies, we are also strengthening our vessel monitoring system at the office. In addition to monitoring the movement of vessels when navigating in piracy-prone areas or narrow waterways with a high risk of collision or running aground, we actively share safety and security information with vessels in the vicinity of shipping routes to support safe navigation and prepare for a quick initial response in the event of an accident. In recent years, typhoons, hurricanes, and cyclones have become larger in intensity and scale and longer in duration, and sharing meteorological information on stormy weather has contributed greatly to reducing the risk of maritime accidents.
Initiatives to Reduce the Rate of Accidents at IMS
At IMS, working under a new organizational structure implemented in FY2022, including establishing an independent safety management department and the integration of marine and engineering operations, we use a variety of metrics to track and investigate the occurrence of accidents, analyze the causes, and strengthen preventative measures to reduce accident rates. In addition, on oceangoing vessels owned and managed by the IINO Group, we have built and continue to operate and maintain a safety management system (SMS) based on the International Safety Management Code (IMS Code) adopted by the International Maritime Organization. The SMS is documented in English and equipped on all vessels after being reviewed by the vessel's flag state (or on their behalf). All crew and the employees of ship management companies conduct operations in accordance with the SMS. The SMS standardizes and clearly defines procedures, including the maintenance of main ship equipment, the practical implements of inspections and the handling of cargo, fuel oil, and dangerous articles, risk management methods for work involving hazards, emergency response in the event of an accident, and the reporting, investigation and recurrence prevention regarding accidents and other incidents including near misses. The PDCA cycle is implemented by periodically revising the SMS and its management status on each vessel to prevent accidents and improve the quality of ship management. In FY2023, frequency of accidents resulting in death or injury (collisions, running aground or fire) was 0.0009 per voyage. The IINO Group will aim to meet its FY2024 goal of zero accidents (collisions, running aground, fire) and continue with efforts to strengthen safety infrastructure and establish a culture of safety.
Data List (Shipping Business: Number of accidents per voyage)
Occupational Health and Safety at IMS
When an occupational accident occurs aboard a ship, IMS carefully investigates the mechanism by which the accident occurred and its causes, formulates recurrence prevention measures that can be easily implemented in the field and disseminates the information among crew members along with training. These efforts are aimed at minimizing the occupational accident frequency rate. In FY2023, the occupational accident frequency rate for IMS crews was 0.292%. We will continue to aim to achive our target of 0.4 or less in FY2024.
Issues Identified through Port State Control
Countries that allow foreign vessels to enter their ports carry out onboard inspections when they arrive to check requirements relating, for example, to equipment and crew qualifications. IMS is working to reduce the number of deficiencies identified through these third-party inspections by enforcing strict safety management in compliance with international regulations.
Data List (Shipping Business: Deficiencies Identified per Port State Control (PSC) Inspection)
Vessel Inspection Performance
Oil Major Inspections
Oil tankers, chemical tankers, and LPG and LNG carriers must undergo and pass vessel inspections conducted by the Oil Companies International Marine Forum (OCIMF), an organization made up primarily of oil major companies around the world, when they transport crude oils and petrochemicals for those companies. These vessel inspections focus on safety aspects listed in items such as ship equipment and the maintenance of various manuals and serve as indicators of safe ship operation.
Data List (Shipping Business: Performance in Oil Major Inspections)
CDI Inspections
Our chemical tankers and LPG carriers are also subjected to vessel inspections conducted by the Chemical Distribution Institution (CDI), which was established by members of the chemical products industry in 1994.
Data List (Shipping Business: Performance in CDI Inspections)
IINO Vessel Inspection System
Day-to-day efforts to ensure safety are crucial for passing external organization vessel inspections. In addition to internal audits required by the safety management system, the IINO Group adopted its own vessel inspection system for all vessels under management in an effort to improve the safety management level. In principle, IINO Vessel Inspections are conducted for each vessel biannually by having a supervisor visit or take passage on a vessel. Since FY2020 we have been making use of remote inspection methods.
Data List (Shipping Business: Performance in Inspections by IINO Vessel Inspection System)
Vessel Inspections to Supervise Safety
The IINO Group dispatches safety superintendents to oil tankers, LPG carriers, and dry bulk carriers that are loading or unloading at Japanese ports. The safety superintendents check the condition of vessel hulls and cargo handling equipment and provide instructions and advice on-site to ensure that unloading work is conducted with sufficient consideration of safety and the environment.
Data List (Shipping Business: Performance in Superintendent Safety Inspections)
Crew Retention
Maintaining a consistently competent crew is essential for achieving safe vessel operation. IMS maintains high crew retention rates by analyzing reasons why crew leave and making improvements.
Customer Satisfaction Surveys
In managing ships, it is important to achieve both reduction of the disbursements, which are expenses for maintenance of vessels, and safe operations, which is to prevent accidents. IMS is contracted by ship owners to perform vessel administrative tasks. IMS carries out customer satisfaction surveys of ship owners once a year and makes improvements in response to points highlighted by the customers. IMS established the Crew Member Training Management Department to develop and enhance crew training and has been working to raise satisfaction ratings by improving the quality of ship management.
Data List (Shipping Business: Customer Satisfaction Level [five-point scale])
Provision of Protective Gear to Group Employees
When the IINO Group employees visit ships, they are loaned protective gear such as helmets, life vests, and goggles by the company to ensure their safety.
Safety in the Real Estate Business
At the six office buildings owned by the IINO Group in the central Tokyo area, we are utilizing the concept of preventive maintenance, which we have cultivated in our Shipping Business, in building management, to prevent accidents and issues before they arise. We are working to secure safety to ensure that we can provide spaces that can be used comfortably and safely by tenants and visitors alike.
BCP Formulation
The IINO Group formulated a Business Continuity Plan (BCP) for continuity and quick recovery of business in the event of a crisis, such as a large-scale disaster or accident. Prompt recovery of building functions during a disaster is essential, and preparations for disasters are also extremely important. We, therefore, implement real estate BCP training assuming a large-scale earthquake every year.
Fire Prevention Management System
Our key lease buildings house many offices. In preparation for the occurrence of disasters such as fires and earthquakes, an association has been formed for fire prevention and disaster prevention, with comprehensive fire drills conducted twice a year. Additionally, we work to secure safety in our buildings through fire risk inspections and disaster management inspections. Our flagship IINO Building has been issued with the Fire Safety Building Certificate (Excellent Mark)* from the Tokyo Fire Department and is operated and managed as a building with superior safety.
* A system of the Tokyo Fire Department to certify buildings with superior fire resistance, such as those that have continued to comply with fire prevention laws and regulations or have conducted measures beyond standards required by laws and regulations, etc. As a result of providing documents, etc., and complying with a type inspection and on-site inspection by the fire station, the IINO Building received certificaiton as an excellent fire prevention building for the third time in 2024 since the first certification in 2018, and it has been authorized to display the Excellent Mark.
Disaster Drills with All Tenants
At the IINO Building and Shiodome Shiba-Rikyu Building, we have been conducting semi-annual evacuation drills with all tenants.
At the IINO Building, we also conduct business continuity plan (BCP) drills (a tabletop drill for first response) semi-annually as part of the drills of the Real Estate Division. These drills aim to ensure that, in case of a disaster, the Emergency Headquarters will be immediately set up at the building and serve as a comprehensive information control headquarters in charge of collecting information about the building and from internal and external sources, giving instructions and making decisions on countermeasures.
In FY2023, the frist drill we conducted was to conefirm the route for removing emergency supplies from the warehouse and to set up a first-aid station. For the second drill, we conducted a hybrid training, combining face-to-face and online sessions, and moved from the office to the location where the emergency headquarters was set up immediately after an occurance of a major earthquake, set up the headquarters, and established a remote communication system. The second drill was a hybrid training session that combined face-to-face and online training.
Data List (Real Estate Business: Types and Frequency of Disaster Drills by Building in FY2023)
Building Security System
Security for facilities, aimed at ensuring safe and comfortable use of the buildings owned by the IINO Group, is provided in cooperation with our Group company, IINO Building Technology Co., Ltd. (IBT). We have adopted two modes of building security: round-the-clock, provided by resident security staff stationed in our buildings, and automated, which dispatches staff when an abnormality is detected through remote monitoring. Additionally, various equipment is installed, including intrusion sensors, the latest security cameras, and the security robots (only at IINO Building) to enable 24-hour monitoring to ensure safety at our buildings. Since July 2024, the security robots have been patrolling some floors at night by calling elevators and moving between floors by themselves.
Monitoring the Status of Accidents and Mishaps
IBT, our building management subsidiary, aims to make buildings owned by the Group safe and convenient to use and strives to make improvements through monthly accident review meetings involving ongoing collection and analysis of data on accidents and other mishaps. Additionally, as a measure to prevent accidents and mishaps from occurring, IBT periodically conducts tests and inspections to maintain the safety of facilities and equipment in buildings owned by the Group.
Data List (Real Estate Business: Number of Accidents/Mishaps)
Occupational Health and Safety at IBT
IBT has established the Health and Safety Committee, which meets monthly. In addition, IBT holds an annual meeting of the Health and Safety Council in cooperation with partner companies to prevent occupational accidents. IBT employees receive semi-annual medical examinations.
Data List (Number of People at IBT Certified as Having Suffered Occupational Accidents)
Employee Safety Training
IBT provides off-the-job (OFF-JT) training sessions designed to improve safety awareness among personnel engaged in building facility management, such as the advanced first aid course and the safety manager course on a regular basis, as well as on-the-job (OTJ) training, such as risk-prediction training, fire and disaster prevention equipment handling training, and emergency radio communication training on a monthly basis, while striving to create a safe workplace environment by performing regular risk assessments.
Qualifications/Training Related to Real Estate
All IBT employees attend the advanced emergency first aid course and have gained advanced emergency first aid certification. Moreover, they have a variety of qualifications and participate in various courses to acquire knowledge about safety and receive training. IBT will continue to promote the training of its employees and their attainment of qualifications.
Provision of Safety Gear
To ensure their safety, employees are loaned protective helmets and other protective gear. We implement initiatives to develop environments in which employees can work with peace of mind.